Avoid Expensive Power Tool Repairs with These 5 Quick Tips
Jul 9th 2019
A large variety of tasks need power tools. They cut, puncture, break and sand all types of materials for all types of reasons. Their importance is immense, as many jobs can only be completed with their help. Many of them are valuable beyond their usefulness—they are also expensive. If power tools are so vital to a job and so expensive to replace, it stands to reason they should be well taken care of.
Here are five ways to maintain power tools and avoid expensive mistakes.
1. Clean your tools regularly.
There are many reasons why cleaning is important—whether it’s power tools or anything else. Clean environments keep up worker morale and a clutter-free workspace lowers the risk of accidents. Those reasons are very important, but let’s focus more on how cleaning specific power tools can help them last longer.
A little dirt or debris on a tool doesn’t do much damage right away, but it can either build up and cause a bigger problem, or it can cause a motor to slightly over-exert itself over a long period of time. Both of these scenarios involve a tool not being cleaned regularly—so regular, frequent cleaning can prevent these scenarios from occurring. Frequent here means it should be cleaned daily if a tool is used more than once a day—and after each use, if it’s used less often. Even if you feel a power tool does not need to be cleaned daily, the act of doing so will make it a good habit and prevent the task from being neglected.
2. Inspect your power tools often.
Whether a power tool is stored away or used daily, routine inspection should be performed. This is mostly for the health of the tool and the people around it. A fixable issue (frayed power cord) can destroy the entire tool. The same issue could also be an electrocution hazard for the operator. How often a tool needs to be inspected varies with how often it’s used and what the tool actually is.
As to what needs to be inspected, a checklist was compiled by OSHA to help.
Here are a few questions you should ask during tool inspection:
- Are power cords free of cracks or burns?
- Do housings display cracks or have loose screws (for high-impact tools)?
- Are the chucks and jaws working properly (for cordless tools)?
- Is any rust building up (for tools used around water)?
- Are there any manufacturer recommended inspections for the tool?
3. Lubricate the gears.
Many power tools need oil or grease to function, but most don’t shut off when the tank is perilously low. Lubrication is very important to keep some tools from breaking down. It is up to the operator to make sure tools are properly oiled or greased. When oil is needed, simply making sure there is enough oil is all that’s needed, but grease is a little more complex.
In general, grease is needed where moving metal pieces come in contact with each other. Periodically re-grease when the tool manufacturer’s recommended time comes up, or if an oil leak is visible. Oil below a tool that only uses grease would indicate that the grease has separated and needs to be cleaned and reapplied.
4. Replace tool parts, as needed.
Power tools have a lot of working parts, and sometimes these parts need to be replaced. Often these parts are designed or expected to fail. Other times a specific part happens to fail unexpectedly, either due to the type of working being done or the environment. In either circumstance, replacing the part quickly can save you a lot of money and time down the road.
If a part was designed or expected to fail (i.e. a filter), then following manufacturer recommended intervals to replace that part is important. Operating a power tool without everything running to its full ability can produce unnecessary strain and cause more expensive parts to fail quicker.
If a part was not expected to fail but did anyways, the earlier section about inspection should help you spot the issue. And once the issue is spotted, it must be rectified quickly. A chain is only as strong as its weakest link, and so a tool is only as effective as its frailest part.
5. Repeat often.
All the above ways to keep your power tools running smoothly only work with constant vigilance. If you forget to clean just one tool after a month of daily usage, it could end up costing you in the end. If you skip a routine inspection because you’re too busy, you could miss an important issue that ends up being ten times the cost. If you misread the signs that a tool needs to be lubricated, or get distracted from checking if a filter needs to be replaced, it could mess up the tool pretty bad, and end up paying for it dearly.
Follow Manufacturer Advice
You may have noticed a theme within each section above. Following these general guidelines will help keep power tools running as they were intended, but specifics are different for different tools. For example, grease is important for hammer drills, but not for cordless drills. Though that is obvious, some other pieces of information might not be so obvious unless the instruction manual is consulted. Different brands of the same tool might even need different upkeep. To make sure a power tool does its job for as long as possible, you need to do your job and keep it properly maintained.
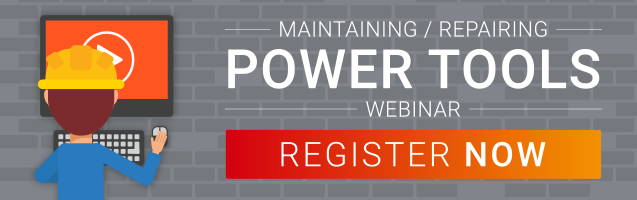